Anilox roll detection
2024-01-03 11:09:47
As we all know, in the flexographic printing process, comprehensive and comprehensive inspection of anilox rollers is very important and necessary for improving the productivity of enterprises. However, many people in the industry did not start. why? what is the reason? The most commonly heard reason is "I don't know what to do." This article aims to teach you how to start from scratch, describes the conditions and content of the anilox roller detection, and how to better detect the anilox roller, so that enterprises can truly improve the quality and reduce consumption, improve production efficiency, and enhance competitiveness. The detection of anilox rollers The purpose of setting up our company and opening factories is to make profits. Since the resources available are very limited, the products produced by the company must meet the requirements of the customers and at the same time be able to make profits for themselves. In order to maintain a sustainable competitive advantage, companies are always trying every means to improve production efficiency, shorten production time, reduce production costs, reduce losses, improve product quality, reduce the number of anilox roller replacement, extend the life of the anilox roller, improve Product consistency, repeatability, and predictability. But where do you start from? After a systematic and fair evaluation of all aspects and factors in the flexographic printing production process, it will be found that the anilox roller is the key and core component in the flexographic printing process. It should start with the tracking detection of the anilox roller to improve the entire The level and quality of the production process. So, what is the detection of the anilox roller? In general, it refers to the use of sophisticated and expensive instrumentation equipment by technical experts to quickly and easily determine the volume, structural condition, and number of screen lines (the number of inked holes in the unit length direction of the anilox roller) of the anilox roller. After the measurement, a report will be obtained, which sometimes includes an image micrograph or a color digital perspective of the ink hole profile. It is very useful to know the current volume of the ink hole on the anilox roller, and you will know if the anilox roller is worn or damaged. However, what we need is not only limited to these, we also need to know the specific location of the damage, and how to better prevent this kind of damage from happening. Because the focus of the problem is all concentrated on the anilox roller, the general inspection is unable to find out the specific damaged parts, and it is impossible to improve the quality of the printed matter while reducing the production cost. Therefore, there is a question that deserves everyone's attention: "What information should we learn from the detection of the anilox roll?" The start of the anilox roll inspection is not only to check the condition of the anilox roll itself, but at the same time, more. It is a comprehensive inspection of the storage, cleaning, processing and operating conditions of the anilox roller. In addition to reducing and preventing defects in the production process, it is also possible to provide a detailed operating list, which is very advantageous for improving the production process. The common mistake people make is to ask an outside helper (technical expert from the manufacturer of the anilox roller) to inspect the anilox roller and check the anilox roller only in isolation. In fact, the detection of anilox rolls is an important part of improving product quality and craftsmanship. Obviously, it is impossible to call the factory technicians to visit the factory every week. In fact, as long as the printing operators are properly trained and require everyone to start from the anilox roller, they can continuously improve the level of technology. After training, the press operator can and should monitor the performance of the anilox roll as a routine task. Required conditions for detection 1. Fixed test site. There should be a stable table or bench that is comfortable and convenient to use, and is best placed next to the cleaning pool. 2. A pair of saddle-shaped roller pads for supporting the anilox roller. The roller pad keeps the anilox roller always at a certain distance from the desk or chair. The bearing can rotate the anilox roller so that the surface of the anilox roller can be safely and completely detected. It is also possible to use a wooden block with a grooved top as a roller pad. If the roller pad is better secured to a wider base, it can prevent accidental tilting and overturning. 3, a good observation of light sources. The light source is an indispensable condition for anilox roller detection. In general, the light source should be placed at a position overlooking the anilox roller and it is easy to adjust. In most workshops, only a fluorescent tube was placed directly above the observation area. In principle, the light in the observation area should be comfortable for inspection of printed proofs. Other necessary tools include a gear removal tool, a 100x magnifying glass, a tape measure, an adhesive mark (used to mark the damaged area on the anilox roller), and a spring blade (used to remove dry residue from the side of the anilox roller), In addition, an irregular trowel is needed (the burrs in the ink hole are flat). If the anilox roller is threaded, buy a set of threaded files. In addition, a set of coded rubber stamps and erasers are needed to distinguish the anilox roller from other rollers adjacent to it. Most anilox rolls have already been marked by the manufacturer with some digital series at the factory. However, after an anilox roll has undergone multiple surface treatments, the roll may eventually be a bunch of expired, useless information. If the press has a side scraper, the side of the anilox roll may wear over time, and the serial number and anilox roll information disappear. After a certain period of time, the serial number of the anilox roller and the number of network lines are re-marked once, so that the information is clearly visible again. Finally, it is worth mentioning that it is also very important to make a log. Use a notebook to record the serial number and screen number of each anilox roller. Any damage to the anilox roller or any visible pattern on the surface should be recorded in the log. , Including the specific location of the damage and the maintenance measures taken against it. In the future, when we need to re-surface the anilox roll, or want to understand the condition of each anilox roll, the log is very convenient. If similar damage is recorded on two or more rollers, it should be marked in red to indicate that the problem is worth investigating. Optional instruments At this point, you are sure to ask: "There is no mention of the equipment used to check the ink holes." Frankly speaking, you do not need these devices at all. If you want to relate prints to the condition of anilox rollers, you don't necessarily need a microscope worth $10,000 or an interferometer worth $60,000. It's not necessary to use these devices. These devices are ideally suited for laboratory applications, and in the pressroom, errors in instrument readings can result from vibration, dust, changes in temperature and humidity, operator errors, and so on. In addition, improper operation can also adversely affect the performance of these precision measuring instruments. If the anilox roller is clean, the dot opening depth and depth of the ink hole and the thickness of the wall can be accurately measured with a dot inspection instrument or an interferometer. On the contrary, if the ink hole is blocked by the ink, the anilox roller will appear blurred, which is often reflected in the ink color of the print. One of the reasons for ambiguity is that the path of light reflected from the translucent resin surface occupies at least part of the volume of the ink hole. These resins contain many pigments and are sufficient to produce a faint color on the surface of the anilox roll. The color of the surface of the anilox roll can be observed with the naked eye without any tools. Well, now you know that the inked hole on the anilox roller is blocked. What other information can be observed with a microscope or an interferometer? Generally speaking, it will not. The dot detector is an optical measuring instrument. After drying, the ink resin will create ambiguity in the ink hole, so that the technician cannot focus clearly. When the ink hole is blocked, the ink hole is observed. The bottom will be blurred. Because the focus cannot be clearly and accurately focused, the depth of the ink hole cannot be accurately measured. When measuring with an interferometer, an interference image is produced as the amount of light reflected from the surface of the ink port changes. This method is sometimes referred to as "echotopography." The blurring of the ink resin will disperse the light and cause the instrument to produce erroneous readings. For example, when measuring the thickness of the wall, if the reading obtained is "0", it is doubtful, because if there is no wall to separate the ink holes, the number of screen lines of the anilox roll must also be determined. Is 0. Another example is the measurement of the number of anilox roller screens. If the reading is 715 before cleaning and 682 after cleaning, this also indicates a problem. Because cleaning does not change the number of inked holes on the surface of the anilox roll, this is simply because the instrument cannot interpret the data received. The safest and most reliable method is to use densitometers to measure density values ​​in the solid, halftone, and highlight areas. The densitometer is an optical measuring instrument that measures the ink transfer performance of an ink hole by a logarithmic operation. The ink transfer performance of the ink hole is not directly related to the amount of ink. The amount of ink transferred is affected by the flow properties of the ink, such as the pH value of the ink, the viscosity, and the size of the pigment particles. In addition, the ambient temperature is also affected. The effect of humidity. During the printing process, as these factors change, even if the ink hole performance remains unchanged, the amount of ink delivered will change. This is not to say that the measuring instrument does not do much for the detection. This simply means that if you want to check if the anilox roll should be cleaned, it is generally not necessary to use these instruments. If the anilox roller looks dirty, it means that cleaning is required; if the anilox roller looks clean, it is generally clean and does not require cleaning.
Advantages of charcoal barbecue:
Big fans of charcoal Stainless Steel Bbq Grill will never choose a gas barbeque. They do have a point: charcoal ovens can reach a ferocious 482 degrees Celsius on the surface of meat, much hotter than standard gas ovens without infrared burners. Using this heat allows the skin of steak and lamb chops to turn into our beloved pastry, while maintaining the red and pink color inside the meat.
Another major advantage of charcoal roasting is smoke, an interesting by-product of burning. Charcoal smoke contains a wide range of flavor molecules, especially when ignited. Gaseous fuels are simple molecules (CH4 is natural gas, C3H8 is liquid propane). If they were completely burned, there would be only water and carbon dioxide, no flavor. In order for a gas oven to produce smoke, wood must be added. When the fat and juice of food drips onto the burning charcoal, a great deal of smoke is produced. If there is only a brief encounter with smoke, it does not significantly alter the flavor of fast-cooking foods such as hot dogs, beef burgers, or even lean steaks. In thick cuts of steak and chicken, the flavor produced by the smoke can be clearly perceived. There is a noticeable difference in flavor if you use your corten steel bbq for a long, low smoke roast. The flavor of the smoke produced by the gas oven is very simple.
Name | Outdoor gas grill corten steel metal barbecue |
Material | Corten steel |
Cooking plate Size | Diameter 1000mm |
Base Size | 500*500*700mm |
Thickness | Base:2mm, Cooking plate:10mm |
Weight | 120KG |
Packing | Pallet/carton/wooden box packing |
Packing
Packing will by pallet/carton/ wooden box,according to different demand.
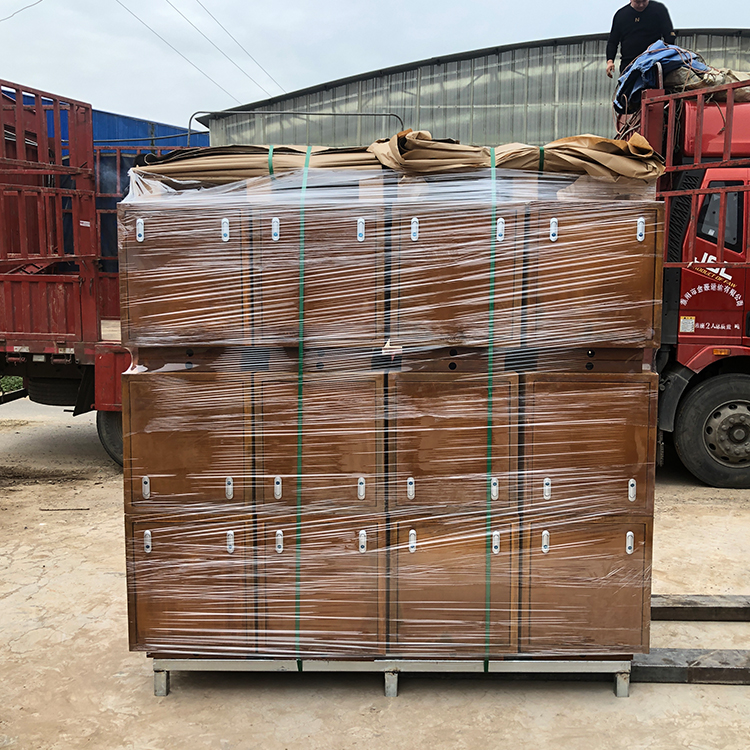
Gas Bbq Grill,Propane Grill,Gas Barbecue,Natural Gas Grill
Henan Jinbailai Industrial Co.,Ltd , https://www.hnjblfirepit.com