What should I do if there is a stepped fault in the transparent plastic box?
2021-11-22 15:07:58
BAIDU_CLB_fillSlot("858283");
In the process of transparent plastic box printing , since the surface smoothness of the film is higher than that of the paper, and a layer of base oil is usually printed first during printing, the film surface has less ink adsorption, and the gradient mesh printing effect is poor, and the ladder is prone to occur. Fault phenomenon. If the prepress design or the plate output is not good, it will further affect the printing effect of the gradient mesh. Below, the author analyzes and discusses the precautions for reducing the occurrence of step faults in the transparent plastic box gradient network printing from the three aspects of computer design process, plate making process and printing process.
Computer design process
(1) Gradient mesh is usually designed with “computer presetâ€. The design should not pull the gradient bar, otherwise it will easily lead to step faults during printing.
(2) Since PostScript only allows 256 gray levels at most, the larger the gradient step size, the more likely the step fault is to occur, so the gradient step should be controlled within a reasonable range.
(3) Minimize the length of the gradient. For the effect of the first real gradient, the solid and gradient parts can be designed separately, and finally connected to reduce the probability of the step fault. The specific design steps are shown in Figure 1-3.
Figure 1 First, make a gradient design
Figure 2 and then do the ground design
Figure 3 Gradient and field synthesis
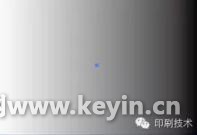
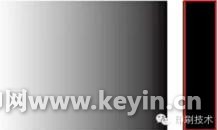
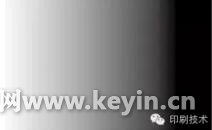
(4) For the gradient network of scanning or color separation , the method of “Gaussian blur + noise processing†can be adopted to reduce the occurrence of step faults.
In the actual work, especially in the proofing stage, our company will check and analyze the design part of the gradient net in the customer's manuscript, and if necessary, design correction on the computer to ensure the printing effect of the gradient net.
Plate making process
(1) The highest output accuracy is used in plate making to reduce the probability of generation of step faults. Normally, CTF plate-making has a maximum output accuracy of 3657 dpi, and CTP plate-making has a maximum output accuracy of 2400 dpi (up to 4800 dpi).
(2) The lower the number of screen lines, the less likely it is that stepped faults will occur. For example, the number of screen lines is usually 175 lines/inch. When a stepped fault occurs in the gradient screen printing, the number of screen lines can be reduced to 150 lines/inch to improve the printing effect.
(3) From the visual analysis, the printing effect when the screen angle is 45° is the smoothest and most natural. Therefore, the spot color gradient net should be designed as a 45° screen angle to reduce the step fault.
(4) for network printing dot gain problem, usually dot gain compensation curve should be adjusted. However, in the case of the gradient mesh design manuscript proofing, straight line publishing will be used to achieve the best gradient effect.
(5) If the concentration and temperature of the sizing machine are too high, it is easy to cause the loss of small dots and increase the risk of stepped faults during the gradient printing. Therefore, our company will reduce the concentration and temperature of the sizing machine properly during the plate making, and increase the development time to compensate for the shortage of the syrup concentration, which can significantly improve the step fault phenomenon.
Printing process
(1) In the printing process, the gradient direction of the gradient mesh should not be the same as the ink path direction.
(2) The pressure of the ink roller should not be too large, otherwise the ink bar will be easily generated when the gradient mesh printing. Therefore, the pressure of the ink roller must be adjusted strictly according to the specified value.
(3) The fourth one relies on the plate roller to absorb the ink, and the pressure can be adjusted to be larger, otherwise the ink collection will be incomplete, and the ink bar will be generated.
(4) The pressure of the water roller should not be too large, otherwise the white bar will be easy to appear on the gradient printing site.
(5) The pH value of the dampening solution is not easy to be low, otherwise it will cause the loss of fine dots during printing and generate step faults.
(6) After the aging of the blanket, the ink cannot be transferred normally, resulting in poor transfer of the fine dots, resulting in a stepped fault. Therefore, the condition of the blanket should be checked regularly and the aging blanket should be replaced in time.
The above content is reproduced in the " Printing Technology " official WeChat (Printech1957) , authorized by the company to publish, copyright, piracy will be investigated !
Upholstery Chair,Office Chair,Multifunctional Round Stool,Fabric Seat
STARWAY INTERNATIONAL HOME-LIVING CO., LTD , https://www.starwayfurniture.com